Understanding Plastic Part Production
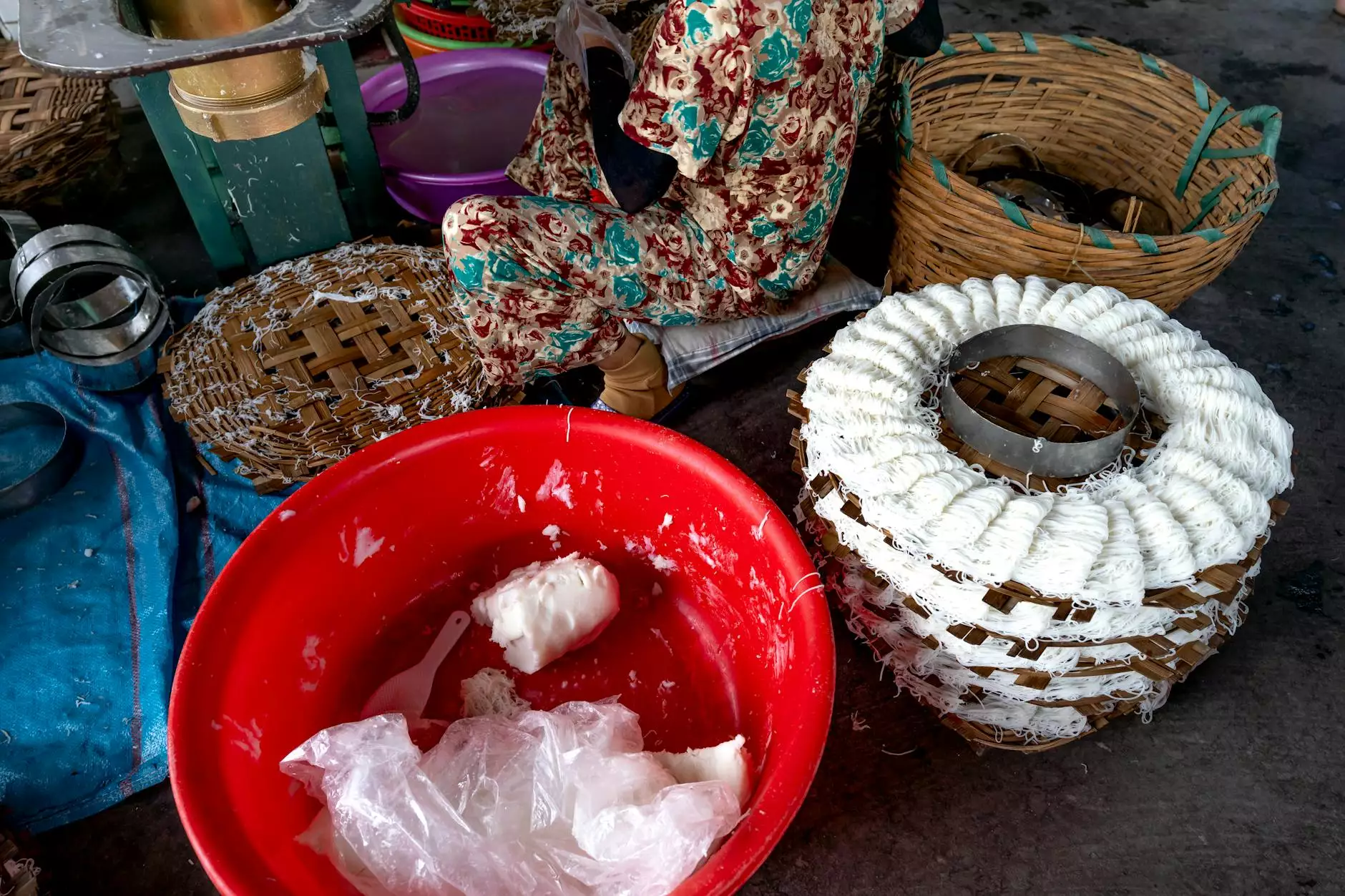
In today's industrial landscape, plastic part production stands as a cornerstone of innovation and efficiency. As businesses increasingly seek ways to improve their manufacturing processes, the ability to produce high-quality plastic components quickly and economically has become more important than ever. This article explores the various facets of plastic part production, detailing its processes, benefits, and the future of manufacturing in this domain.
What is Plastic Part Production?
Plastic part production encompasses a variety of processes used to create parts and components from plastic materials. These processes are vital in multiple industries, including automotive, aerospace, consumer goods, and electronics. The primary goal is to achieve precision, durability, and efficiency in creating parts tailored to specific applications.
The Key Processes in Plastic Part Production
Several core manufacturing processes are utilized in the production of plastic parts. Each method has its unique advantages, making it suitable for different applications. These include:
- Machining
- Laser Cutting
- Welding
- Plastic Injection Molding
- Vulcanization
1. Machining
Machining involves removing material from a solid block of plastic to create the desired shape. It’s a subtractive manufacturing process that includes methods such as turning, milling, and drilling. This technique is highly accurate and allows for the production of complex geometries.
2. Laser Cutting
Laser cutting uses focused laser beams to cut or engrave plastic materials. This method offers significant precision and is often employed in creating intricate designs. Its advantages include minimal waste and the ability to produce detailed parts rapidly, making it ideal for prototyping.
3. Welding
Welding in plastic part production refers to the fusion of plastic components through various techniques like ultrasonic welding and hot plate welding. This method is perfect for assembling different plastic parts, producing strong and reliable joints that can withstand various stresses.
4. Plastic Injection Molding
Injection molding is arguably the most widely used method for producing plastic parts. This process involves injecting molten plastic into a mold, where it cools and solidifies into the final part. It is highly efficient for mass production, allowing for complex designs while ensuring uniformity and high-quality output.
5. Vulcanization
Vulcanization is a chemical process that transforms plastic materials by introducing sulfur or other agents to enhance their properties. This method is particularly suitable for rubber-like plastics, increasing their strength and durability, making them ideal for high-performance applications.
The Benefits of Plastic Part Production
The manufacturing of plastic parts offers numerous advantages that can significantly enhance operational efficiency and product quality. Some of these benefits include:
- Cost-Effectiveness - Utilizing plastic allows manufacturers to reduce material costs while maintaining quality.
- Lightweight - Plastic parts are generally lighter than their metal counterparts, contributing to lower transportation costs and improved fuel efficiency in vehicles.
- Corrosion Resistance - Plastics are naturally resistant to rust and corrosion, making them suitable for harsh environments.
- Design Flexibility - Modern manufacturing techniques provide the flexibility to create complex designs easily.
- Fast Production Rates - Techniques like injection molding allow for rapid mass production with minimal waste.
Innovations in Plastic Part Production
The field of plastic part production is constantly evolving with advancements in technology. New materials, processes, and methods continue to emerge, influencing how manufacturers approach production. Recent innovations include:
3D Printing
3D printing, or additive manufacturing, has revolutionized plastic part production. This method allows for the creation of highly customized parts without the need for expensive molds. Businesses can quickly prototype designs, test functionality, and iterate on ideas rapidly.
Biodegradable Plastics
As environmental awareness grows, the demand for sustainable materials is on the rise. Biodegradable plastics offer a solution by reducing the ecological footprint of plastic production. Companies focusing on eco-friendly manufacturing are becoming leaders in the industry.
Smart Plastics
Smart plastics are embedded with electronic components that allow them to interact with their environment. These materials can be used in applications ranging from smart packaging to advanced medical devices, showcasing the endless possibilities of innovative plastic production.
The Future of Plastic Part Production
As we move forward, the future of plastic part production looks promising. With increasing automation and the integration of artificial intelligence, manufacturers can optimize production lines for efficiency and quality. Continuous research and development in materials science will further expand the potential applications of plastics across different industries.
Challenges in Plastic Part Production
Despite its advantages, the production of plastic parts is not without challenges. Manufacturers must navigate:
- Material Costs - Fluctuating oil prices can impact the cost of plastic materials.
- Environmental Impact - Traditional plastic production is under scrutiny due to its contribution to global pollution.
- Regulatory Compliance - Manufacturers must keep abreast of laws governing plastic production and waste management.
Conclusion
In conclusion, plastic part production plays a vital role in various industries, providing a flexible, economical, and innovative manufacturing solution. With ongoing advancements and a focus on sustainability, the future of this field is robust. Companies like Sumiparts are at the forefront of this industry, offering services such as machining, laser cutting, welding, plastic injection, and vulcanization. By embracing innovation and adapting to industry trends, manufacturers can continue to thrive and meet the evolving demands of the market.