Die Casting Machine Manufacturer: Transforming Metal Fabrication
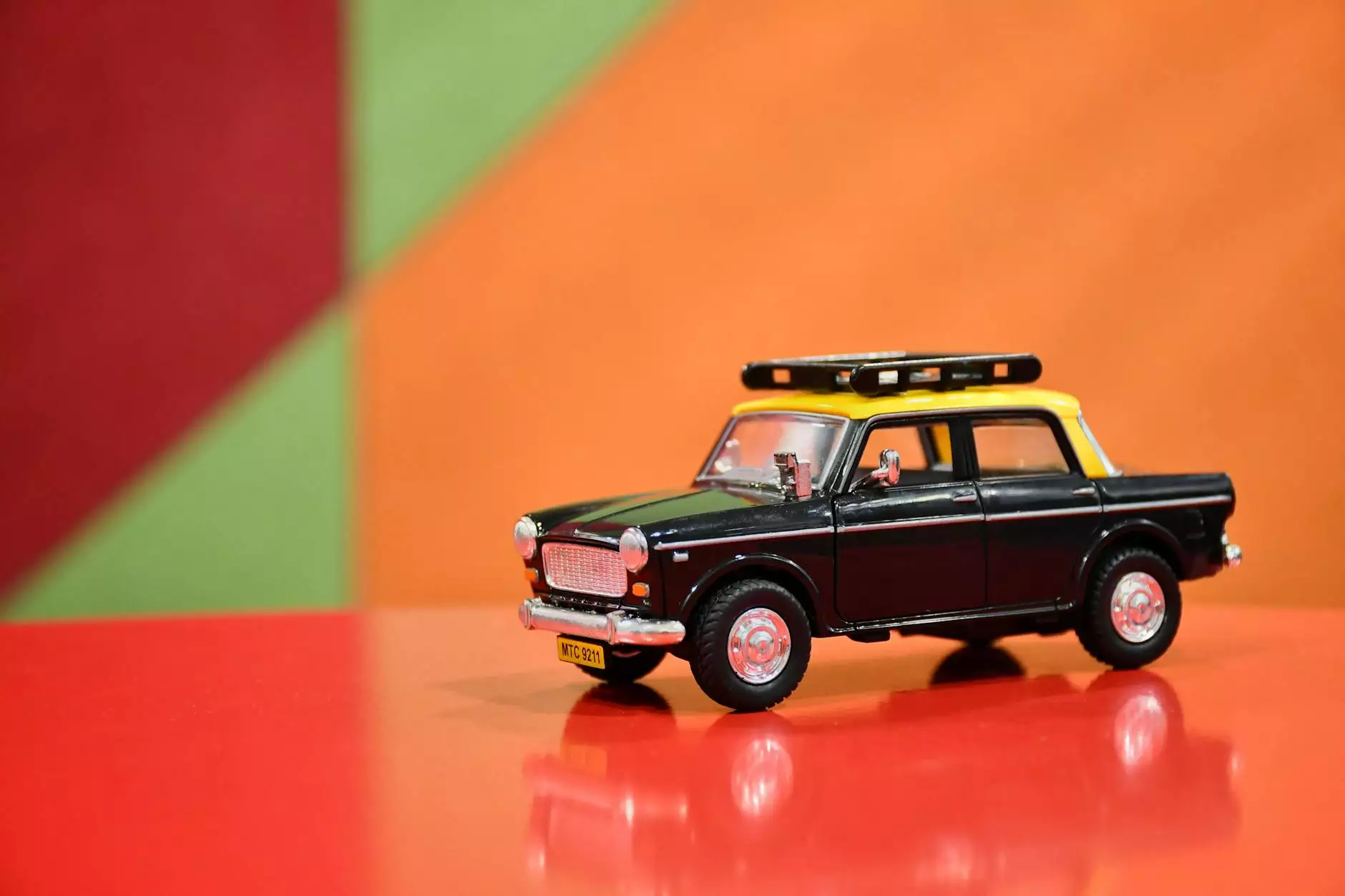
Die casting is a manufacturing process that is vital for producing high-quality metal parts with incredible precision. As industries evolve, the role of a die casting machine manufacturer becomes increasingly critical in delivering the tools necessary for efficient and effective production. In this article, we will delve deep into the world of die casting, exploring its benefits, the technology involved, and how to choose the right manufacturer to meet your needs.
Understanding Die Casting
Die casting is a metal casting process that forces molten metal into a mold cavity under high pressure. This technique has been widely adopted in various industries due to its ability to produce complex shapes with very tight tolerances. The die casting process is characterized by the following:
- High efficiency: Die casting can produce thousands of parts in a short time span, making it an economical choice for mass production.
- Exceptional accuracy: Parts produced through die casting typically feature superior surface finishes and dimensional consistency.
- Material versatility: Various metals, such as aluminum, zinc, and magnesium, can be used, offering numerous material properties to suit different applications.
The Benefits of Die Casting
Choosing die casting as your manufacturing process offers several key advantages:
1. Cost-Effectiveness
Due to its high production rates, die casting can significantly lower manufacturing costs compared to other methods. The initial investment in die casting machines may seem high, but the reduction in finishing and assembly time ultimately leads to greater savings.
2. Superior Surface Quality
Parts produced through die casting often require minimal post-processing, resulting in excellent surface finishes that reduce additional expenses and time delays.
3. Strength and Durability
Products made from die casting exhibit superior strength and durability due to the high pressure used during the casting process, resulting in a denser and more reliable final product.
4. Scalability
The die casting process can be easily scaled to meet the needs of varying production levels, making it ideal for both small runs and large-scale manufacturing.
Types of Die Casting Machines
Understanding the different types of die casting machines available is essential for any business looking to incorporate this process:
1. Hot Chamber Die Casting Machines
This type of machine is suitable for metals with low melting points, such as zinc and aluminum. The melting pot is an integral part of the machine, allowing for quick transitions between casting cycles.
2. Cold Chamber Die Casting Machines
Cold chamber machines are preferred for metals with high melting points, like aluminum. Here, the molten metal is poured into the chamber manually, which increases the machine's versatility in handling various materials.
Choosing the Right Die Casting Machine Manufacturer
Selecting a reputable die casting machine manufacturer is crucial for ensuring that your production needs are met efficiently and effectively. Consider the following factors:
1. Reputation and Experience
Look for manufacturers with a proven track record in the industry. Companies with extensive experience are more likely to understand your specific requirements and provide high-quality machines tailored to your operations.
2. Quality of Machinery
Investigate the quality standards of the machines they produce. Ensure that the manufacturer adheres to international standards and uses high-grade materials, enhancing the lifespan of your machinery.
3. Support and Maintenance
Consider the after-sales support and maintenance services provided by the manufacturer. A reliable manufacturer will offer comprehensive support to ensure that your machines operate smoothly.
The Role of Deepmould.net in the Die Casting Industry
At Deepmould.net, we pride ourselves on being a leading die casting machine manufacturer with a commitment to excellence in the metal fabrication industry. Our extensive range of die casting machines is designed to meet the diverse needs of various sectors, including automotive, aerospace, and consumer goods.
Why Choose Deepmould.net?
- Innovative Technology: Our machines incorporate the latest technological advancements, ensuring optimal performance and efficiency.
- Customized Solutions: We work closely with clients to develop tailored solutions that align with their specific production requirements.
- Skilled Team: Our team of experts is dedicated to providing exceptional service and support throughout the entire process.
Future Trends in Die Casting
The die casting industry is continually evolving, and staying abreast of the latest trends is essential for manufacturers:
1. Automation and Industry 4.0
The integration of automation in die casting processes is growing. Modern die casting machines now come equipped with smart technologies, enabling real-time monitoring and control to optimize production.
2. Sustainable Practices
As industries face increasing pressure to adopt sustainable practices, manufacturers are looking at die casting processes that reduce waste and energy consumption. Environmentally friendly materials and recycling methods are gaining traction.
3. Advanced Materials
Research into advanced and lightweight materials is creating opportunities for the die casting industry, particularly in sectors like aerospace and automotive, where performance and fuel efficiency are paramount.
Conclusion
In conclusion, the role of a die casting machine manufacturer is pivotal in advancing the metal fabrication industry. Understanding the die casting process, its benefits, and how to select the right manufacturer will empower businesses to make informed decisions that drive efficiency and profitability. With companies like Deepmould.net leading the charge, the future of die casting looks bright, promising advancements that will continue to reshape manufacturing as we know it.