Understanding the Significance of Silicone Membrane for Vacuum Forming
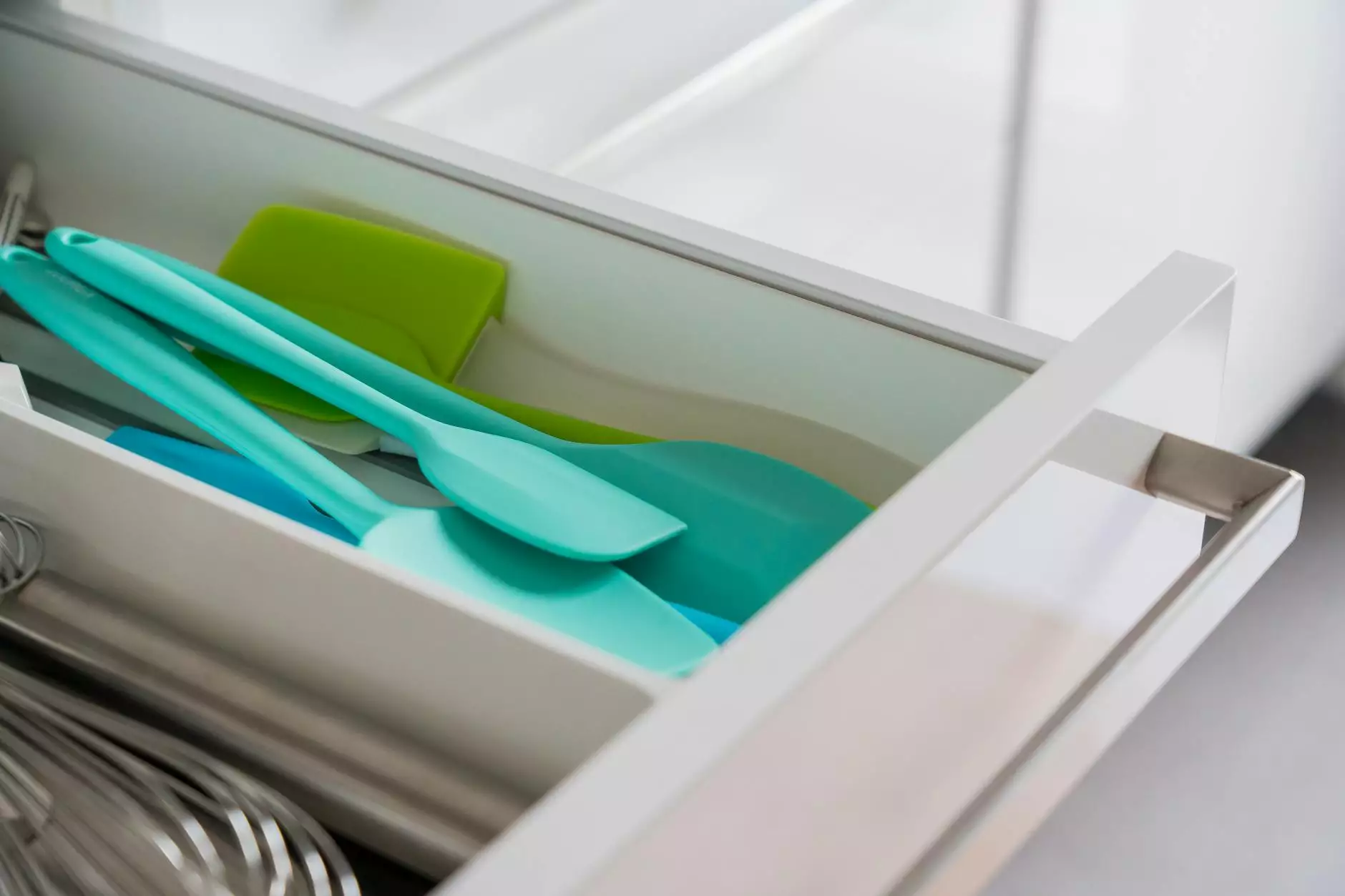
In today's rapidly evolving manufacturing landscape, the quest for effective production techniques is paramount. One such advancement that captures the attention of industries is the silicone membrane for vacuum forming. This innovative solution has transformed how products are designed, prototyped, and produced, offering a range of benefits that can enhance quality, reduce waste, and improve efficiency.
What is Vacuum Forming?
Vacuum forming is a plastic molding technique where a heated plastic sheet is shaped over a mold using vacuum pressure. This method is widely used across various industries, including automotive, packaging, and consumer goods, thanks to its efficiency in producing detailed and complex shapes. The process typically involves the following steps:
- Material Heating: A thermoplastic sheet is heated until pliable.
- Mold Placement: The heated sheet is placed over a mold.
- Vacuum Application: Vacuum pressure is applied to draw the sheet tightly over the mold.
- Cooling: The material cools and solidifies into the desired shape.
- Trimming and Finishing: The formed part is trimmed and finished for its final use.
The Role of Silicone Membranes in Vacuum Forming
The introduction of silicone membranes into the vacuum forming process marks a significant innovation. Silicone membranes are designed to effectively transfer vacuum pressure while providing exceptional durability and flexibility. Here are several reasons why integrating silicone membranes can benefit businesses:
1. Enhanced Durability
Silicone membranes are crafted from high-quality silicone rubber, making them resistant to tears, punctures, and other types of wear and tear. This durability ensures that the membranes have a long lifespan, allowing businesses to save on replacement costs and reduce downtime.
2. Superior Flexibility
The flexibility of silicone membranes allows them to adapt to various shapes and sizes during the forming process. This adaptability is crucial for producing intricate designs and structures without compromising the quality of the final product.
3. High-Temperature Resistance
Silicone can withstand high temperatures, which is critical during the heating phase of vacuum forming. This quality allows for the processing of a wider range of materials without risk of damage, further expanding the potential applications.
4. Improved Sealing Capabilities
A good seal is essential in vacuum forming to create the necessary pressure for molding. Silicone membranes provide excellent sealing properties that enhance vacuum retention, leading to higher-quality finished products.
5. Chemical Resistance
Silicone’s resistance to many chemicals also makes membranes suitable for use with various materials, further enhancing the versatility of the vacuum forming process.
Applications of Silicone Membranes in Business
Businesses across various sectors can significantly benefit from incorporating silicone membranes for vacuum forming into their production lines. Here’s a closer look at some applications:
1. Appliance Manufacturing
The appliance industry relies heavily on vacuum forming for producing components such as panels, casings, and trays. Using silicone membranes can improve the manufacturing process of these parts by providing better precision and finish.
2. Home Cleaning Products
In the home cleaning sector, products like vacuum cleaners and specialty cleaning tools often require custom-shaped plastic components. Utilizing silicone membranes can enhance the quality and functionality of these products, enabling manufacturers to meet consumer demands for efficiency.
3. Automotive Components
The automotive industry uses vacuum forming for parts such as dashboards, trims, and interior components. Employing durable silicone membranes helps in maintaining the quality and consistency of these parts, which is vital in automotive applications.
4. Packaging Solutions
Effective packaging is crucial for product protection and branding. Silicone membranes can enhance the vacuum forming process in creating packaging products that are both functional and appealing to consumers.
Benefits of Using Silicone Membranes for Vacuum Forming in Business
Businesses that adopt silicone membranes for their vacuum forming processes can expect numerous benefits:
- Cost Efficiency: The durability of silicone membranes reduces the frequency of replacements, thereby saving costs over time.
- Higher Quality Products: Enhanced sealing and pressure retention improve the overall quality and integrity of the formed products.
- Versatility: Silicone membranes can be used with a variety of materials and shapes, allowing companies to expand their product lines.
- Quicker Production Times: The efficiency of the vacuum forming process is improved with silicone membranes, which can lead to higher output rates.
- Eco-Friendliness: Less waste is generated during the forming process as silicone helps in creating precise shapes, fostering sustainability in production.
How to Choose the Right Silicone Membrane?
When selecting a suitable silicone membrane for vacuum forming, several factors should be considered:
1. Thickness and Durability
Choose a membrane thickness that aligns with the products being produced. Thicker membranes are often more durable but may be less flexible, while thinner options can be more pliable but less robust.
2. Temperature Resistance
Select membranes that can withstand the heating requirements of your specific applications to avoid deformation during use.
3. Compatibility with Materials
Ensure the chosen silicone membrane is compatible with the types of plastics and chemicals involved in the vacuum forming process.
4. Cost and Availability
Analyze the cost-effectiveness of your chosen membranes and ensure they are readily available to avoid production delays.
Conclusion: Unlocking Business Potential with Silicone Membranes
In closing, the integration of silicone membranes for vacuum forming represents a groundbreaking advancement for businesses in various industries. By leveraging the unique properties of silicone, companies can enhance their production capabilities, improve product quality, and maintain competitive advantages in their markets. As businesses continue to innovate and adapt, embracing advanced materials and technologies will undeniably play a crucial role in achieving lasting success.
For further inquiries and to explore the best silicone membrane options for your vacuum forming needs, visit vacuum-presses.com, where we provide comprehensive solutions tailored to your business requirements.